目次
1.ピッキングミスでお困りのお客様へ
これまで部品ピッキングの支援システムは、リストピッキングや、デジタルピッキングシステム(以下DPS)が主流でした。
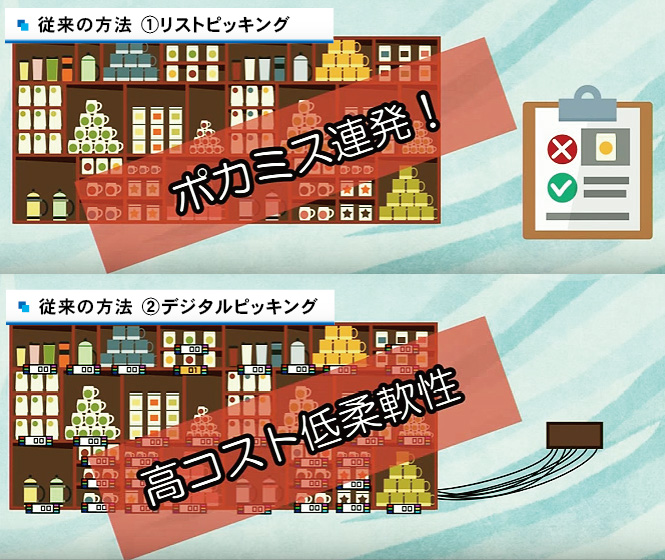
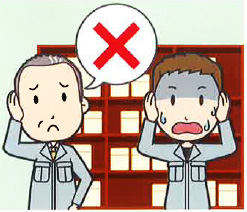
多くの部品を使用するため、どれだけ入念・綿密なチェックをしていても、月間5~6件のミスが発生することも。
うち、数ヶ月に1度はミスをスルーし、後工程のラインが止まる事態を招いてしまうお客様もいらっしゃいます。
また、デジタルピッキングでは、多くの配線や工事の施工が必要で、棚のレイアウト変更は大掛かりな作業でした。
うち、数ヶ月に1度はミスをスルーし、後工程のラインが止まる事態を招いてしまうお客様もいらっしゃいます。
また、デジタルピッキングでは、多くの配線や工事の施工が必要で、棚のレイアウト変更は大掛かりな作業でした。
2.レーザーを使った「次世代型の部品ピッキングシステム」をおすすめします!
今回ご紹介する、株式会社ナ・デックスの「レーザーピッキングシステム」は、レーザーを指示器として利用した次世代の部品ピッキング支援システムです。
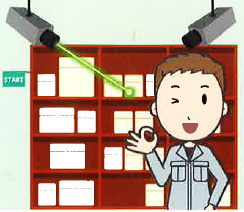
なんとミスが0件に!
ラインを止めるような大きなミスはもちろん、小さな部品取得ミスも無くなり、作業効率が格段にアップしました。
ピッキングリストも廃止、さらに休憩時間の短時間で簡単に棚のレイアウト変更が可能になりました。
ラインを止めるような大きなミスはもちろん、小さな部品取得ミスも無くなり、作業効率が格段にアップしました。
ピッキングリストも廃止、さらに休憩時間の短時間で簡単に棚のレイアウト変更が可能になりました。
【1】システム概要
【手順1】上位システム又はCSVより、ピッキング部品情報を取得します。【手順2】ピッキング指示データを作成し、最適なピッキング経路順に並び替えます。
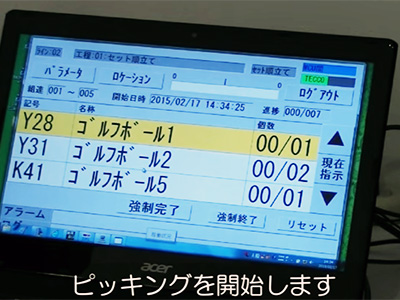
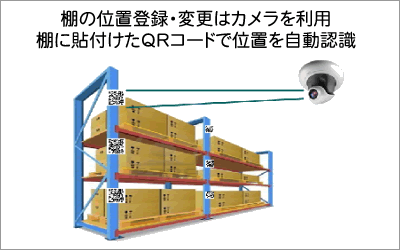
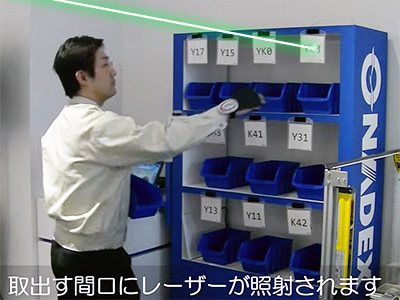
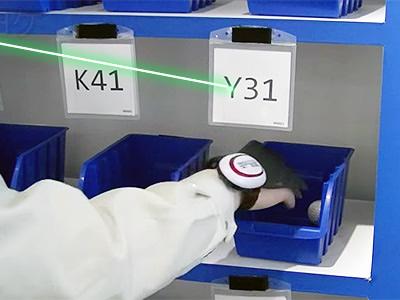
【2】動画でわかり易くご覧いただけます
【3】レーザーピッキングシステム5つのおすすめポイント!
【1.誤品不良ゼロ】手甲型RFIDリーダを利用して「取りポカ」に対応します。
間違った間口に手を入れると、RFIDリーダが振動することで、作業者に間違いを気づかせます。
部品投入時や、部品箱セット時の「入れポカ」にも対応します。
手甲型RFIDリーダが振動することで、作業者に間違いを気づかせます。
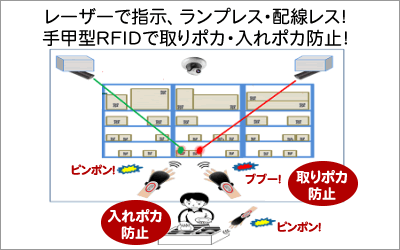
【2.作業効率化・作業者支援】
作業者に対して、率の良い動線順にレーザーが指示を出して導きます。
部品位置を覚えていない初心者でも、簡単に作業できます。
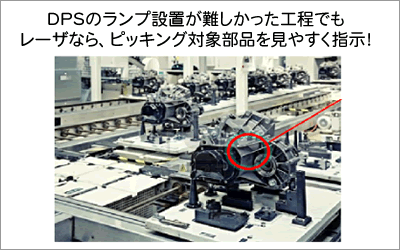
【3.配線レス・棚レイアウト変更】
DPSと異なりランプ配線、工事施工が不要です。
このため、たな位置の変更にすぐ対応できます。
多品種少量生産時代に最適な部品ピッキングシステムです。
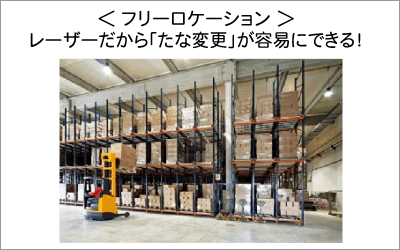
【4.両手で作業ができる】
ハンディリーダーを使わないので、両手で作業ができます。
【5.DPSと比べてメンテナンスが容易】
DPSでは棚の数だけランプを管理する必要がありましたが、レーザーピッキングシステムではランプ管理が不要になりますので、管理コストが下がります。
【まとめ】
大手自動車メーカー様、自動車部品メーカー様(ティア1)で実績があり、その他企業様でも導入検討中いただいております。製造工程や、物流における部品ピッキング作業全般にオススメですので、自動車業界以外のお客様もぜひお問合わせください!